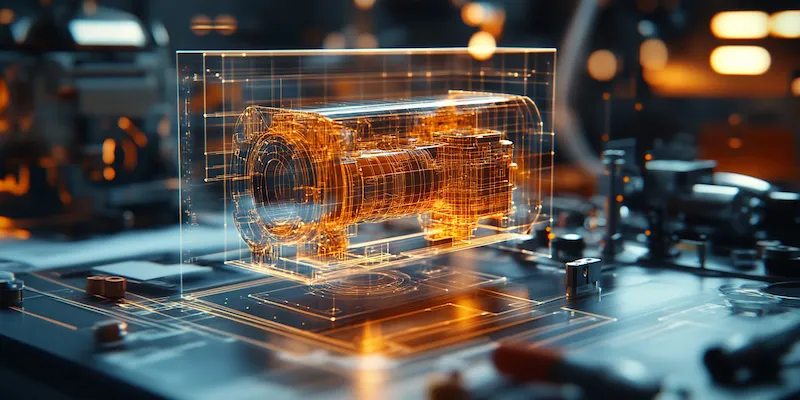
Budowa maszyn pneumatycznych opiera się na kilku kluczowych elementach, które współdziałają ze sobą, aby zapewnić efektywne działanie systemów pneumatycznych. Wśród najważniejszych komponentów znajdują się sprężarki, które odpowiadają za wytwarzanie sprężonego powietrza. Sprężarki mogą być różnego rodzaju, w tym tłokowe, śrubowe czy wirnikowe, a ich wybór zależy od specyficznych potrzeb aplikacji. Kolejnym istotnym elementem są zbiorniki ciśnieniowe, które magazynują sprężone powietrze i pozwalają na jego równomierne dostarczanie do układów roboczych. W systemach pneumatycznych niezbędne są również zawory sterujące, które regulują przepływ powietrza oraz ciśnienie w układzie. Zawory te mogą być ręczne lub automatyczne, co wpływa na wygodę i efektywność pracy urządzenia. Dodatkowo, w budowie maszyn pneumatycznych istotną rolę odgrywają siłowniki pneumatyczne, które przekształcają energię sprężonego powietrza w ruch mechaniczny. Siłowniki te mogą mieć różne kształty i rozmiary, co pozwala na ich zastosowanie w różnych aplikacjach przemysłowych. Ostatnim ważnym elementem są przewody pneumatyczne, które transportują sprężone powietrze między poszczególnymi komponentami systemu.
Jakie zastosowania mają maszyny pneumatyczne w przemyśle
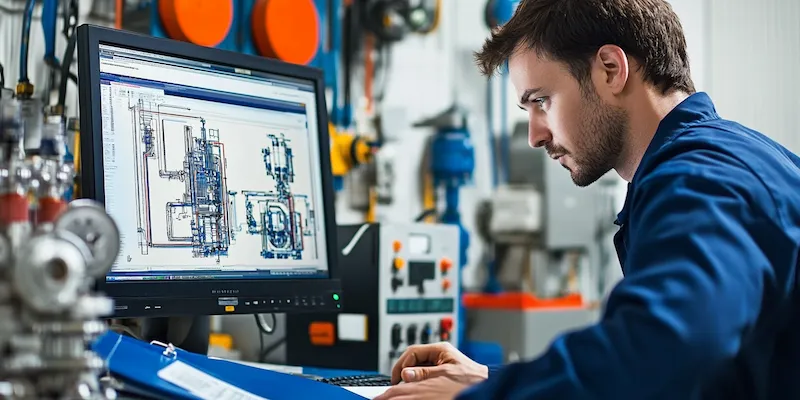
Maszyny pneumatyczne znajdują szerokie zastosowanie w różnych branżach przemysłowych, co czyni je niezwykle wszechstronnymi narzędziami. W przemyśle produkcyjnym wykorzystuje się je do automatyzacji procesów montażowych, gdzie precyzyjne ruchy siłowników pneumatycznych przyspieszają produkcję i zwiększają jej efektywność. W branży motoryzacyjnej maszyny pneumatyczne są wykorzystywane do podnoszenia ciężkich elementów oraz do precyzyjnego montażu podzespołów. W sektorze spożywczym maszyny te służą do pakowania produktów oraz transportu surowców w zamkniętych systemach, co zapewnia higieniczne warunki pracy. W budownictwie natomiast maszyny pneumatyczne są używane do zasilania narzędzi ręcznych, takich jak młoty udarowe czy wiertarki, co znacznie ułatwia wykonywanie prac budowlanych. Dodatkowo w branży medycznej maszyny pneumatyczne znajdują zastosowanie w urządzeniach diagnostycznych oraz terapeutycznych, gdzie precyzyjne dawkowanie powietrza jest kluczowe dla bezpieczeństwa pacjentów.
Jakie są zalety stosowania maszyn pneumatycznych
Stosowanie maszyn pneumatycznych wiąże się z wieloma korzyściami, które przyczyniają się do zwiększenia efektywności procesów przemysłowych. Przede wszystkim maszyny te charakteryzują się dużą niezawodnością oraz prostotą obsługi, co sprawia, że są idealnym rozwiązaniem dla wielu aplikacji przemysłowych. Dzięki zastosowaniu sprężonego powietrza jako medium roboczego, maszyny pneumatyczne są bezpieczniejsze od tych elektrycznych czy hydraulicznych, ponieważ nie grożą wyciekiem cieczy ani porażeniem prądem. Ponadto sprężone powietrze jest łatwo dostępne i tanie w eksploatacji, co obniża koszty operacyjne związane z użytkowaniem tych urządzeń. Maszyny pneumatyczne są również bardzo elastyczne i mogą być łatwo integrowane z innymi systemami automatyki przemysłowej. Dzięki temu możliwe jest szybkie dostosowanie ich do zmieniających się potrzeb produkcyjnych. Kolejną zaletą jest ich wysoka prędkość działania oraz zdolność do generowania dużych sił przy niewielkich rozmiarach urządzeń. To sprawia, że maszyny pneumatyczne idealnie nadają się do zastosowań wymagających precyzyjnego i szybkiego ruchu.
Jakie wyzwania stoją przed budową maszyn pneumatycznych
Budowa maszyn pneumatycznych wiąże się z różnymi wyzwaniami technicznymi oraz organizacyjnymi, które należy uwzględnić podczas projektowania i wdrażania tych systemów. Jednym z głównych problemów jest konieczność zapewnienia odpowiedniej szczelności układów pneumatycznych, ponieważ nawet niewielkie nieszczelności mogą prowadzić do strat energii oraz obniżenia efektywności działania całego systemu. Dlatego tak ważne jest stosowanie wysokiej jakości materiałów oraz precyzyjne wykonanie połączeń między komponentami. Kolejnym wyzwaniem jest dobór odpowiednich parametrów pracy maszyn pneumatycznych, takich jak ciśnienie robocze czy wydajność sprężarek. Niewłaściwe ustawienia mogą prowadzić do awarii lub niewłaściwego działania urządzeń. Również konieczność regularnej konserwacji i serwisowania maszyn stanowi istotny aspekt ich eksploatacji; zaniedbanie tego procesu może skutkować kosztownymi naprawami lub przestojami produkcyjnymi. Dodatkowo zmieniające się normy prawne dotyczące bezpieczeństwa pracy oraz ochrony środowiska stawiają przed producentami nowych maszyn dodatkowe wymagania dotyczące ich konstrukcji oraz użytkowania.
Jakie są najnowsze technologie w budowie maszyn pneumatycznych
W ostatnich latach w budowie maszyn pneumatycznych pojawiły się liczne innowacje technologiczne, które znacząco poprawiają ich wydajność oraz funkcjonalność. Jednym z najważniejszych trendów jest rozwój systemów sterowania opartych na technologii IoT, co pozwala na zdalne monitorowanie i zarządzanie pracą maszyn. Dzięki temu operatorzy mogą na bieżąco śledzić parametry pracy urządzeń, co umożliwia szybką reakcję na ewentualne problemy oraz optymalizację procesów produkcyjnych. Kolejnym istotnym kierunkiem rozwoju jest zastosowanie sztucznej inteligencji w analizie danych zbieranych przez maszyny pneumatyczne. Algorytmy AI mogą przewidywać awarie, co pozwala na przeprowadzenie konserwacji prewencyjnej i minimalizację przestojów. Warto również zwrócić uwagę na nowoczesne materiały stosowane w budowie komponentów pneumatycznych, takie jak kompozyty czy stopy metali o wysokiej wytrzymałości, które zwiększają trwałość i niezawodność urządzeń. Dodatkowo, rozwijają się technologie związane z produkcją sprężarek, które stają się coraz bardziej energooszczędne i ciche, co ma kluczowe znaczenie w kontekście ochrony środowiska oraz komfortu pracy.
Jakie są koszty związane z budową maszyn pneumatycznych
Koszty związane z budową maszyn pneumatycznych mogą być zróżnicowane i zależą od wielu czynników, takich jak skomplikowanie projektu, wybór komponentów oraz wymagania dotyczące wydajności. Na początku procesu projektowania istotne jest określenie budżetu, który będzie obejmował zarówno koszty materiałów, jak i robocizny. W przypadku prostych układów pneumatycznych koszty mogą być relatywnie niskie, jednak bardziej zaawansowane systemy wymagają znacznych nakładów finansowych na zakup wysokiej jakości komponentów oraz technologii sterowania. Dodatkowo należy uwzględnić wydatki związane z instalacją oraz uruchomieniem maszyn, które mogą wiązać się z koniecznością przeszkolenia personelu obsługującego urządzenia. Koszty eksploatacji maszyn pneumatycznych również powinny być brane pod uwagę; obejmują one wydatki na energię elektryczną potrzebną do zasilania sprężarek oraz regularne konserwacje i naprawy. Warto również pamiętać o potencjalnych oszczędnościach wynikających z automatyzacji procesów produkcyjnych, które mogą znacznie zwiększyć efektywność pracy i obniżyć koszty operacyjne w dłuższej perspektywie czasowej.
Jakie są przyszłe kierunki rozwoju maszyn pneumatycznych
Przyszłość maszyn pneumatycznych zapowiada się obiecująco dzięki ciągłemu rozwojowi technologii oraz rosnącemu zapotrzebowaniu na automatyzację procesów przemysłowych. Jednym z kluczowych kierunków rozwoju jest dalsza integracja systemów pneumatycznych z technologiami cyfrowymi, co pozwoli na jeszcze większą automatyzację i optymalizację procesów produkcyjnych. W miarę jak przemysł 4.0 staje się rzeczywistością, maszyny pneumatyczne będą musiały dostosować się do wymagań inteligentnych fabryk, gdzie komunikacja między urządzeniami będzie kluczowa dla efektywności działania całego zakładu. Ponadto rosnąca świadomość ekologiczna sprawia, że producenci maszyn będą poszukiwali rozwiązań bardziej przyjaznych dla środowiska; może to obejmować rozwój technologii sprężarek wykorzystujących odnawialne źródła energii lub systemy odzysku ciepła generowanego podczas pracy maszyn. Warto również zauważyć rosnące zainteresowanie miniaturyzacją komponentów pneumatycznych; mniejsze siłowniki i zawory mogą znaleźć zastosowanie w coraz bardziej skomplikowanych aplikacjach wymagających ograniczonej przestrzeni.
Jakie są różnice między maszynami pneumatycznymi a hydraulicznymi
Maszyny pneumatyczne i hydrauliczne to dwa różne typy systemów stosowanych w automatyce przemysłowej, które mają swoje unikalne cechy oraz zastosowania. Główna różnica między nimi polega na medium roboczym; maszyny pneumatyczne wykorzystują sprężone powietrze jako źródło energii, podczas gdy maszyny hydrauliczne działają na zasadzie cieczy hydraulicznych. To sprawia, że maszyny pneumatyczne są lżejsze i łatwiejsze w obsłudze, a także mniej podatne na wycieki czy korozję. Z drugiej strony maszyny hydrauliczne charakteryzują się większą siłą roboczą oraz zdolnością do wykonywania bardziej skomplikowanych ruchów; dlatego często znajdują zastosowanie tam, gdzie wymagana jest duża moc lub precyzyjne sterowanie ruchem. Kolejną różnicą jest koszt eksploatacji; sprężone powietrze jest zazwyczaj tańsze niż cieczy hydrauliczne, co czyni maszyny pneumatyczne bardziej ekonomicznymi w dłuższej perspektywie czasowej. Warto również zwrócić uwagę na różnice w konserwacji obu typów systemów; maszyny pneumatyczne wymagają mniej regularnej konserwacji niż hydrauliczne, które często muszą być kontrolowane pod kątem wycieków oraz jakości oleju hydraulicznego.
Jakie są najczęstsze problemy związane z użytkowaniem maszyn pneumatycznych
Użytkowanie maszyn pneumatycznych może wiązać się z różnymi problemami technicznymi, które mogą wpływać na ich efektywność oraz niezawodność działania. Jednym z najczęstszych problemów są nieszczelności w układzie pneumatycznym; nawet niewielkie wycieki powietrza mogą prowadzić do znacznych strat energii oraz obniżenia wydajności całego systemu. Dlatego tak ważne jest regularne kontrolowanie szczelności połączeń oraz wymiana uszczelek czy innych elementów eksploatacyjnych. Innym powszechnym problemem jest niewłaściwe ciśnienie robocze; zarówno zbyt wysokie, jak i zbyt niskie ciśnienie może prowadzić do awarii lub niewłaściwego działania siłowników czy zaworów. Użytkownicy powinni regularnie monitorować parametry pracy swoich urządzeń oraz dostosowywać je do wymagań aplikacji. Ponadto awarie sprężarek to kolejny częsty problem związany z użytkowaniem maszyn pneumatycznych; ich niewłaściwa eksploatacja lub brak konserwacji może prowadzić do uszkodzeń mechanicznych czy spadku wydajności sprężania powietrza. Ważne jest również dbanie o odpowiednią jakość sprężonego powietrza; obecność wilgoci czy zanieczyszczeń może negatywnie wpłynąć na działanie układów pneumatycznych i skrócić żywotność komponentów.